... Dr.-Ing. Andreas Menne und Dipl.-Ing. Tim Schulzke vom Fraunhofer UMSICHT
Interview vom 30.08.2021
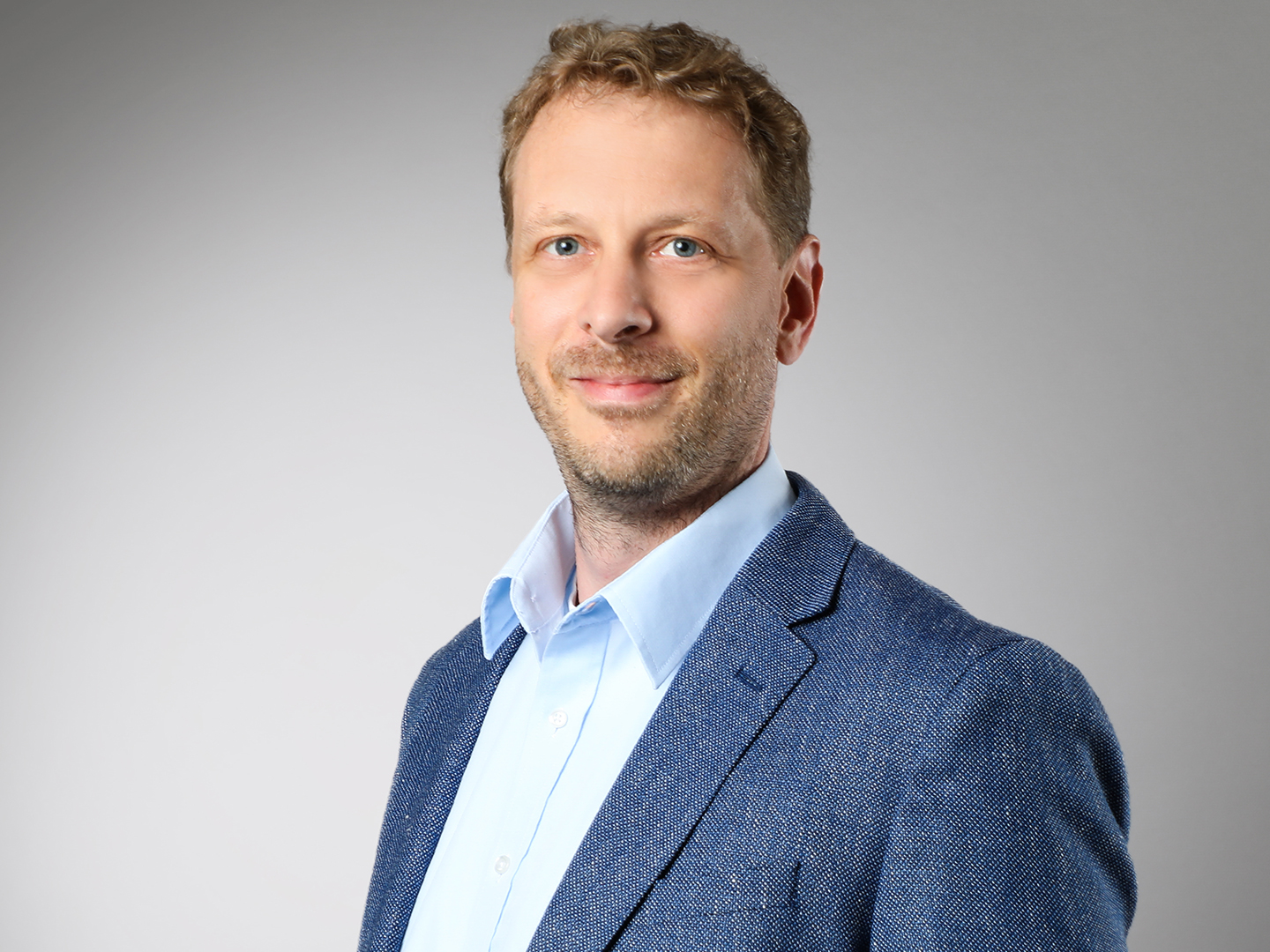
Als Wissenschaftler des Fraunhofer UMSICHT arbeiten Sie in der angewandten Forschung und beschäftigen sich im Verbundprojekt mit der Methanolsynthese. Was wurde aus dieser Perspektive betrachtet bislang in Carbon2Chem® erreicht?
Andreas Menne: Im Rahmen von Carbon2Chem® sollen Gasgemische, die bei der Stahlherstellung anfallen, genutzt werden, um mit Hilfe von Wasserstoff aus erneuerbarem Strom Produkte für die chemische Industrie und synthetische Kraftstoffe herzustellen. Eine sehr vielversprechende Substanz, die sich so herstellen lässt, ist Methanol. Es ist eine der weltweit meistgenutzten Chemikalien und kann auch als Kraftstoff oder in der Kraftstoffherstellung genutzt werden. Die besondere Herausforderung im Projekt liegt darin, das Methanol mit Gasgemischen herzustellen, die heute so nicht verwendet werden. Die Herstellung muss dabei möglichst effizient ablaufen und CO2 einsparen, damit ein insgesamt nachhaltiger und wirtschaftlicher Prozess entsteht.
Mit diesen Vorgaben haben wir vor etwa fünf Jahren begonnen, die Methanolsynthese mit Hüttengasen zu untersuchen. Angefangen bei Versuchen im Labormaßstab mit verschiedenen möglichen Gasgemischen bestehend aus CO, CO2, N2 und H2 wurden zunächst Versuche zur Untersuchung der Betriebsparameter Druck, Temperatur und Gasmengenstrom durchgeführt. Parallel dazu wurden Modelle erstellt, um die Methanolsynthese auch in einer Prozesssimulation darstellen zu können. Vom Labormaßstab mit Flaschengasen sind wir über einen Zwischenschritt nun in der Lage, eine Demonstrationsanlage mit einer Kapazität von ca. 2 l/h Methanol zu betreiben und diese im Modell sehr gut nachzubilden. Beides kann nun genutzt werden, um die nächsten Schritte in Richtung einer flexibleren Produktion zu gehen und dabei sowohl Methoden als auch Werkzeuge der Digitalisierung zu nutzen. So führen wir Simulation und experimentelle Untersuchungen im Demonstrationsmaßstab zusammen und sind in der Lage, Wirtschaftlichkeit und CO2-Ersparnis auszurechnen und den Betrieb einer Produktionsanlage zu optimieren. Ebenso konnte mit einer Laboranlage ein über mehrere Monate dauernder Betrieb mit gereinigten Gasen aus dem Stahlwerk erfolgreich durchgeführt werden. Das hat es bislang weltweit vermutlich noch nicht allzu oft gegeben.
Diese Ergebnisse sind für einen Zeitraum von fünf Jahren sehr beachtlich, da es nicht immer einfach ist, die Interessen aller Partner zu berücksichtigen. Gelingt aber in einem nächsten Schritt eine weitere Maßstabsvergrößerung (basierend auf den bisherigen Ergebnissen), besitzt die Technologie das Potenzial, enorme Mengen CO2 aus Industriegasen zu binden und ein Produkt herzustellen, welches gleichzeitig unsere Mobilität sichert und als Basischemikalie zum Beispiel in der Baustoffherstellung eingesetzt werden kann.
Tim Schulzke: An verschiedenen kleinskaligen Versuchsanlagen wurden im Labor sowohl mit reinen Flaschengasen als auch mit gereinigten Hüttengasen viele Erkenntnisse zum Verhalten des Katalysators gewonnen. Zur Übertragung der Erkenntnisse auf eine Anlage im Produktionsmaßstab ist eine Anlagenkonfiguration erforderlich, die möglichst nahe an den Betriebsbedingungen einer solchen Produktionsanlage arbeitet. Dazu konnte in Phase 1 (6/2016 – 5/2020) eine gebrauchte Containeranlage zur Demonstration der Methanolsynthese beschafft werden. Die wesentlichen Merkmale einer Produktionsanlage wie Kreislaufführung nicht umgesetzter Einsatzgase und Reaktorkühlung über einen Siedewasserkreislauf sind bei dieser Anlage vorhanden. Da diese gebrauchte Anlage ursprünglich für andere Gaszusammensetzungen ausgelegt war, musste sie für den Einsatz mit Hüttengasen modifiziert werden. Auch für die weitere Digitalisierung der Anlage wurden Maßnahmen umgesetzt (u.a. die Portierung der gesamten Steuerung auf eine neuere Hardware und Software), da auf dem ursprünglichen System die geplanten Datenbearbeitungen und Regelalgorithmen nicht mehr anwendbar waren.
Was waren Highlights?
Andreas Menne: Der kontinuierliche Betrieb der Demonstrationsanlage, welche für ein Forschungsinstitut schon eine beachtliche Größe (zwei Seecontainer) besitzt, war ein Highlight. Insbesondere, da die guten Ergebnisse aus den vorherigen Versuchen im Labormaßstab bestätigt werden konnten und auch die Ergebnisse aus der Prozesssimulation die Realität offenbar sehr genau abgebildet haben. Mindestens genauso spannend war der Betrieb der Laboranlage mit gereinigten Gasen aus dem Stahlwerk über mehrere Monate. Mit beiden Anlagen konnte die technische Machbarkeit des Verfahrens grundsätzlich nachgewiesen werden.
Tim Schulzke: Auch wenn noch nicht alles vollständig wie beabsichtigt funktioniert hat, war das mit Abstand größte Highlight die 5-wöchige Versuchskampagne im Dauerbetrieb, d.h. rund um die Uhr, im Juni/Juli 2021 nach mehreren Jahren der Ertüchtigung (Abnahme- und Erlaubnisfähigkeit), Anpassung der gebrauchten Anlage an die im Projekt vorliegenden Anforderungen und Vorbereitung der Steuerung und Messdatenerfassung auf die Maßnahmen zur Digitalisierung unter dem Stichwort Industrie 4.0 – z.B. modellbasierte Regelung oder die datenbasierte Wartung.
Was waren die größten Herausforderungen?
Andreas Menne: In einem so großen Projekt ist insbesondere der Austausch zwischen einzelnen Arbeitsgruppen nicht immer einfach. Vor allem, wenn teils gegenläufige Arbeitsweisen aus Unternehmen und Forschung überein gebracht werden müssen. Eine große Herausforderung besteht noch darin, jetzt den nächsten Schritt zu einer industriellen Produktionsanlage zu begleiten. Die Wirtschaftlichkeit einer solchen Anlage ist noch stark von politischen Rahmenbedingungen und auch einer gewissen öffentlichen Förderung abhängig. Trotzdem ist eine solche Weiterentwicklung zwingend notwendig, wenn wir als Gesellschaft zukünftig CO2 neutral wirtschaften wollen.
Tim Schulzke: Die Containeranlage zur Demonstration der Methanolsynthese ist eine gebrauchte Anlage. Die größte Herausforderung war die vollständige und regelungskonforme Dokumentation zum Explosionsschutz, um die Gesamtanlage in einen abnahmefähigen Zustand zu versetzen. Für einige der älteren Geräte, die in der Anlage verbaut waren, wurde die entsprechende Dokumentation nicht mitgeliefert und sie konnte auch beim jeweiligen Hersteller nachträglich nicht mehr ausgestellt werden. Daher mussten einige Geräte ausgetauscht werden.
Welche nächsten Schritte sind geplant?
Andreas Menne: Als nächster Schritt ist der Betrieb der Demonstrationsanlage mit gereinigtem Gas aus dem Stahlwerk geplant. Idealerweise mehrere Monate im Dauerbetrieb. Dies wird nochmal weitere Erkenntnisse für die Auslegung und den Betrieb einer Produktionsanlage bringen. Gleichzeitig werden wir versuchen, die Ergebnisse aus der Prozesssimulation und den Betrieb der Anlage noch mehr miteinander zu verbinden. Hierfür haben wir begonnen, einen so genannten »digitalen Zwilling« der Anlage zu erstellen. Damit soll es zukünftig möglich sein, die Anlage so zu steuern, dass vorausschauend auf schwankende Randbedingungen wie Wasserstoffverfügbarkeit, schwankende Gasmengenströme und Gaszusammensetzungen reagiert werden kann. Gleichzeitig können so notwendige Wartungsintervalle, zum Beispiel um den Katalysator zu wechseln oder zu regenerieren, geplant werden.
Tim Schulzke: Nach einer weiteren Versuchskampagne mit der Demonstrationsanlage mit reinen Flaschengasen in Oberhausen wird der Container nach Duisburg an das Carbon2Chem®-Technikum umgesetzt und dort für den Rest der Projektlaufzeit (bis Mai 2024) mit realen Gasen aus der Hüttengasaufbereitung betrieben.