... Dr.-Ing. Heiko Lohmann and Dr. Thomas Wiesmann from Fraunhofer UMSICHT
Interview of 07.10.2021
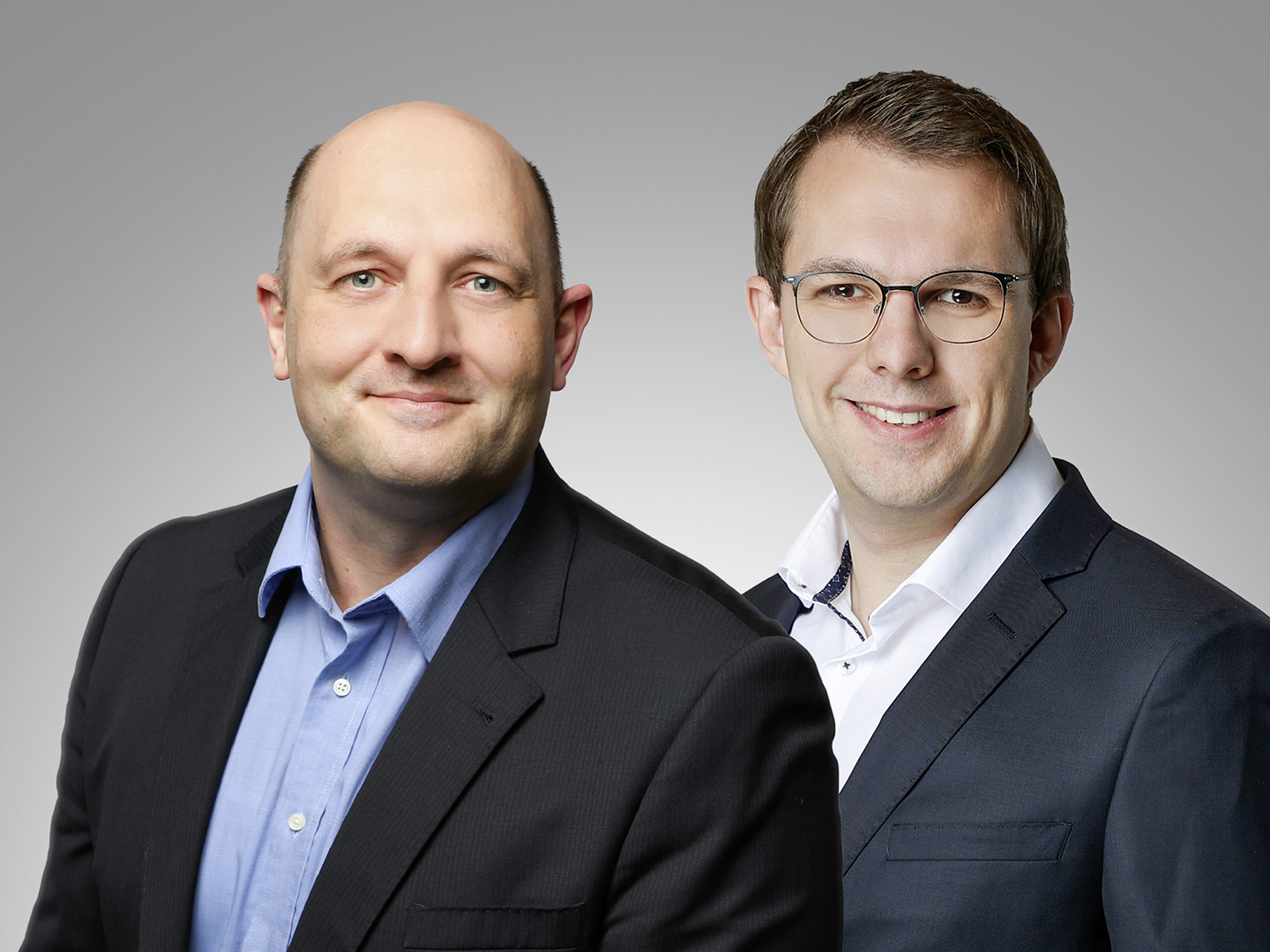
As scientists at Fraunhofer UMSICHT, you work in applied research and you are involved in the research project in the context of catalyst development and testing. What has been achieved so far in this area within Carbon2Chem®?
Heiko Lohmann: Through extensive catalyst testing at the sites in Oberhausen and Sulzbach-Rosenberg as part of subproject L-IV, Fraunhofer UMSICHT has helped project partner Evonik Operations GmbH in Hanau with the ongoing further development of the heterogeneous catalysts for higher alcohol synthesis, starting with the first generation catalysts. Compared to the first generation, the current second generation catalysts have significantly better alcohol selectivities combined with simultaneous elimination of undesirable reaction products. This is an important step on the way to creating a cost-effective process for producing higher alcohols from metallurgical gases.
Thomas Wiesmann: In Carbon2Chem® we have managed to get many industry partners and research institutions to collaborate together to achieve the major objective of a more climate-friendly steel industry. I think the biggest advantage of such a research project is that it pools expertise from different fields of technology. Research work as a whole can thus be driven forward more effectively in order to deliver valuable key technologies for a more sustainable steel industry as quickly as possible.
With regard to catalyst development, we were able to tackle the complex and laborious process together and focus on different aspects at the same time but with the common goal of a new catalyst system. In this way, the project consortium has succeeded in developing the basis for a new catalyst system for synthesizing oxygenates (alcohols) and olefins within the space of five years.
What have been the highlights?
Heiko Lohmann: As UMSICHT project manager for subproject L-IV, one stand-out highlight for me is the commitment of the UMSICHT team who conduct the extensive catalyst tests at the Oberhausen and Sulzbach-Rosenberg sites. Not only do our colleagues perform and evaluate the test series, which is very complex and time-consuming given the large volumes of data involved, they also adapt the test plants to the changing demands of a dynamic project. Another highlight for me is the trusted and constructive collaboration of the project consortium which brings together expertise in industry and science. This excellent level of cooperation is something special and is crucial when it comes to achieving the aims of Carbon2Chem®.
Thomas Wiesmann: As a young engineer, I have been especially excited by the technical processes, test plants and analytical devices. At the start of the project, we had to plan, design and commission new test benches or convert existing ones within a short period of time. I never imagined at the start of the project that constantly developing and optimizing these devices on the basis of the latest findings would play such an essential role. Looking back, however, this was/is one of the most important factors that allows us to be so successful in the area of catalyst testing. Particularly in the field of analytics, we have managed through continual improvements to exploit the complex product spectrum of catalysts and to draw conclusions from this about how the catalysts function.
What were the biggest challenges?
Heiko Lohmann: The biggest challenge our team faces is the day-to-day experimental work. Ensuring that the plants are available for the catalyst tests means that any technical defects that occur in them have to be remedied or any necessary conversion work has to be performed as quickly as possible. Constantly further developing the accompanying analytics to record the reaction products in as much detail as possible should not be underestimated either and is very time-consuming.
Thomas Wiesmann: In terms of catalyst testing, the biggest challenge was to analyze many catalysts in a short space of time. The technical term for this process is catalyst screening. Catalyst screening always requires a balancing act between rapidly testing many catalysts and analyzing the synthesis products as extensively and accurately as possible. Since this project involves investigating completely new catalyst systems for this application, every hour spent testing is valuable to learn more about these systems. The time needed for repairing, maintaining or converting the test benches and devices needs to be kept to a minimum, so that we lose as little testing time as possible.
Because one thing is for sure: As unique and technically sophisticated as our test benches might be, complex technical defects can also occur. Just like your dishwasher or washing machine at home, our devices also sometimes have “aches and pains” which need to be diagnosed and cured quickly and systematically.
What are the next steps?
Heiko Lohmann: The next steps include catalyst tests under application-oriented conditions. This includes further investigations into shaped catalyst bodies as would later be used in a technical process. We will focus on testing shaped catalyst bodies with model gases to investigate the influence of shaping on mass and heat transfer, for example.
Thomas Wiesmann: So far, the project consortium has succeeded in identifying a suitable catalyst material/powder and in shaping it. Shaping is needed because the use of catalyst powders on an industrial scale would lead to excessive pressure losses in the reactors. The last step before industrial use is therefore investigating the shaped catalyst bodies. These tests are critical as we are taking the leap from laboratory plants (ideal boundary conditions in terms of heat and mass transfer) to industry-like conditions. Just like in the lab, we will first carry out these investigations using high-purity gases from gas cylinders, before finally testing the catalysts with real gas, i.e., purified gases from the Duisburg steel mill. This will show us not only whether the entire project has succeeded in developing a promising catalyst, which in itself would be a huge success from a scientific viewpoint, but also whether it will succeed in making steel production more sustainable.