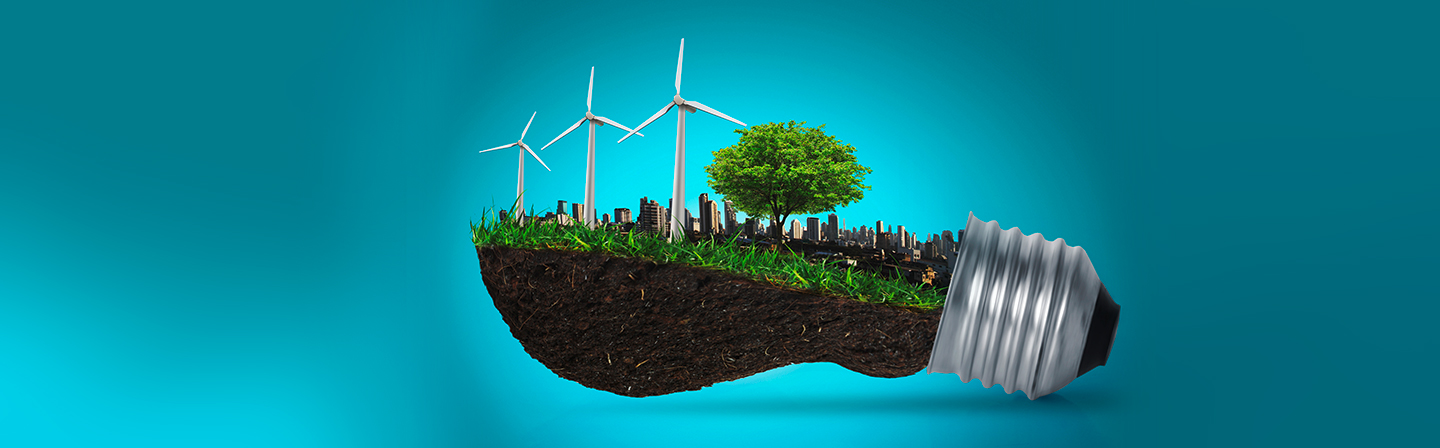
Together with industrial partners, the department develops technologies and solutions in the field of sector coupling with a focus on cross-industrial systems. The avoidance, reduction and utilization of CO2 is a major goal of the work. The technology development is supported by process simulations and higher-level system integration, planning and optimization. To this end, the department uses methods and tools of digitization such as simulation-based control, predictive maintenance, reverse modeling, co-simulation, and digital twin, thus combining experimental process development, process simulation, and system analysis.
In technology development, chemical technologies and gas purification or supply form two main topics. These include the provision of hydrogen and carbon sources (CO/CO2) for syntheses as well as the transport and necessary logistics and utilization of the gases on a systemic level. The department is able to map complete value chains – from raw materials and their processing to the synthesis of products such as fuels or basic materials for industry. The digitization, optimization, flexibilization and dynamization of processes are the goals of the developments.
The Chemical Technologies Group develops processes and products from sustainable raw materials and residues. We use catalytic processes to generate chemicals and fuels that can replace non-sustainably produced products in the short to medium term. We use automated laboratory plants (mini-plants) for process development, which can also be operated at high temperatures and under high pressure. In addition to synthesis, we also deal with purification of the product mixtures and further refinement in downstream chemical processes. In our work, we combine thermal processes such as fast pyrolysis and gasification of biobased feedstocks with catalytic processes such as methanol synthesis, from gas streams that fluctuate in quantity and composition, or the production of higher alcohols from methanol, ethanol, or isopropanol. The products can be used as fuels for ships, vehicles and - after a further hydrogenation step - even as jet fuel.
The importance of special processes for gas purification will grow strongly in a circular economy. In particular, the demand for hydrogen and the use of CO- or CO2-containing gas streams are decisive factors here. The working group is particularly concerned with gas purification processes such as temperature and pressure swing adsorption. One focus is on work on the thermal regeneration of adsorbents or filters with Electric Swing Adsorption (ESA). In this way, an adsorbent can be regenerated particularly energy-efficiently and quickly. The process is suitable, for example, for the separation of trace components from gas streams, but also for the separation of CO2 from air.
In addition to process development, the working group also carries out material developments and process simulations tailored to the processes.
Other topics include, for example, the purification of gases (H2/CH4) from cavern storage facilities, the treatment of gas streams containing ammonia, and the separation of CO/N2 mixtures.
The implementation of the energy turnaround and the necessary transformation steps for climate-neutral industry will no longer be solved to the necessary extent on a sector- or industry-specific basis alone. Rather, the defossilization of processes, the use of renewable energies and the use of renewable raw materials will only be possible by linking the energy and material flows of different production systems.
Our work here focuses in particular on the design and systemic consideration of cross-industrial production systems, as implemented in the context of Carbon Capture and Utilization (CCU) and PTX solutions.
Efficient simulations offer insights that are very time-consuming and cost-intensive to achieve using conventional experimental methods. The appropriate choice of model is a key to success. Our portfolio ranges from the creation of real models to abstract mathematical formulations.
Information material of the department Low Carbon Technologies | Reference projects of the department Low Carbon Technologies