... Martin Peters from Fraunhofer UMSICHT
Interview of 17.11.2021
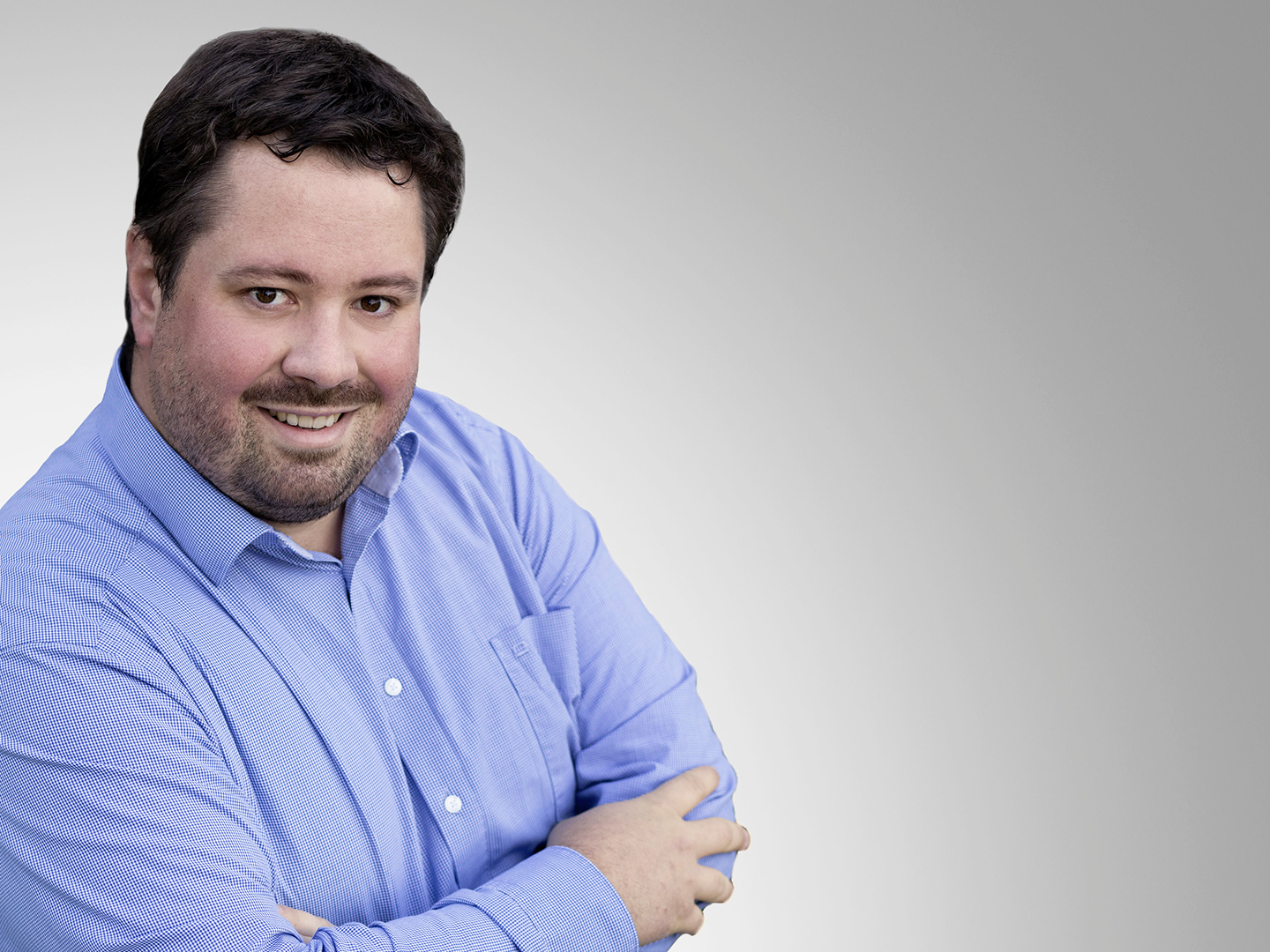
As a scientist at Fraunhofer UMSICHT, you work in applied research and you are involved in the research project in the context of gas purification and use. What has been achieved so far in this area within Carbon2Chem®?
Martin Peters: In subproject L-III we are looking at the purification of metallurgical gases with various processes. One such process is electric swing adsorption (ESA) which we use to adsorb high-boiling hydrocarbons from the coke oven gas. ESA is unique in that the necessary heating, regeneration or desorption of the hydrocarbons is brought about by the electrical resistance of the adsorbent. For this, electric current flows through the adsorbent. The ESA process has to date mainly been investigated scientifically in the laboratory. Here, for example, various adsorbents such as shaped bodies, granulates and pellets were tested for their technical feasibility and economic viability. It was shown that by simply changing the design of the adsorption vessels, low-cost activated carbon pellets with very good technical properties can be used.
What have been the highlights?
Martin Peters: The foundation trials in the first phase of the project allowed us to collect data and findings which can be applied to the ESA technology on a larger scale. A particular success was therefore the commissioning of a pilot plant at the Duisburg site, where real coke oven gas can now be treated. This allows us to verify the previous results on real gas and optimize the system further.
What were the biggest challenges?
Martin Peters: It was challenging not to go with the technically simplest solution but to have to take economic aspects for larger scale systems directly into account. For example, the form of the adsorbents I just mentioned. During the lab tests, the performance was excellent for heating in the case of honeycomb bodies like those used in car exhaust catalytic converters or diesel particulate filters. But these are difficult to get hold of in larger dimensions for subsequent technical use and are expensive. So, we had to completely redesign the adsorber vessel we had used previously in order to be able to use inexpensive adsorbents in the form of pellets with adequate performance.
What are the next steps?
Martin Peters: The next step is to extend the use of ESA to other areas of application. Special adsorbents will be developed in the further course of Carbon2Chem® which, in addition to having good properties for heating, will also be functional. These will allow various components to be separated from the different metallurgical gases which can be used as materials in other subprojects. If the lab results are good then the adsorbents will also be tested on a larger scale in the pilot plant on real metallurgical gases.