…Dr. Julian Schittkowski and Dr. Oliver Hegen from the Max Planck Institute for Chemical Energy Conversion (MPI-CEC)
Interview of 02.08.2021
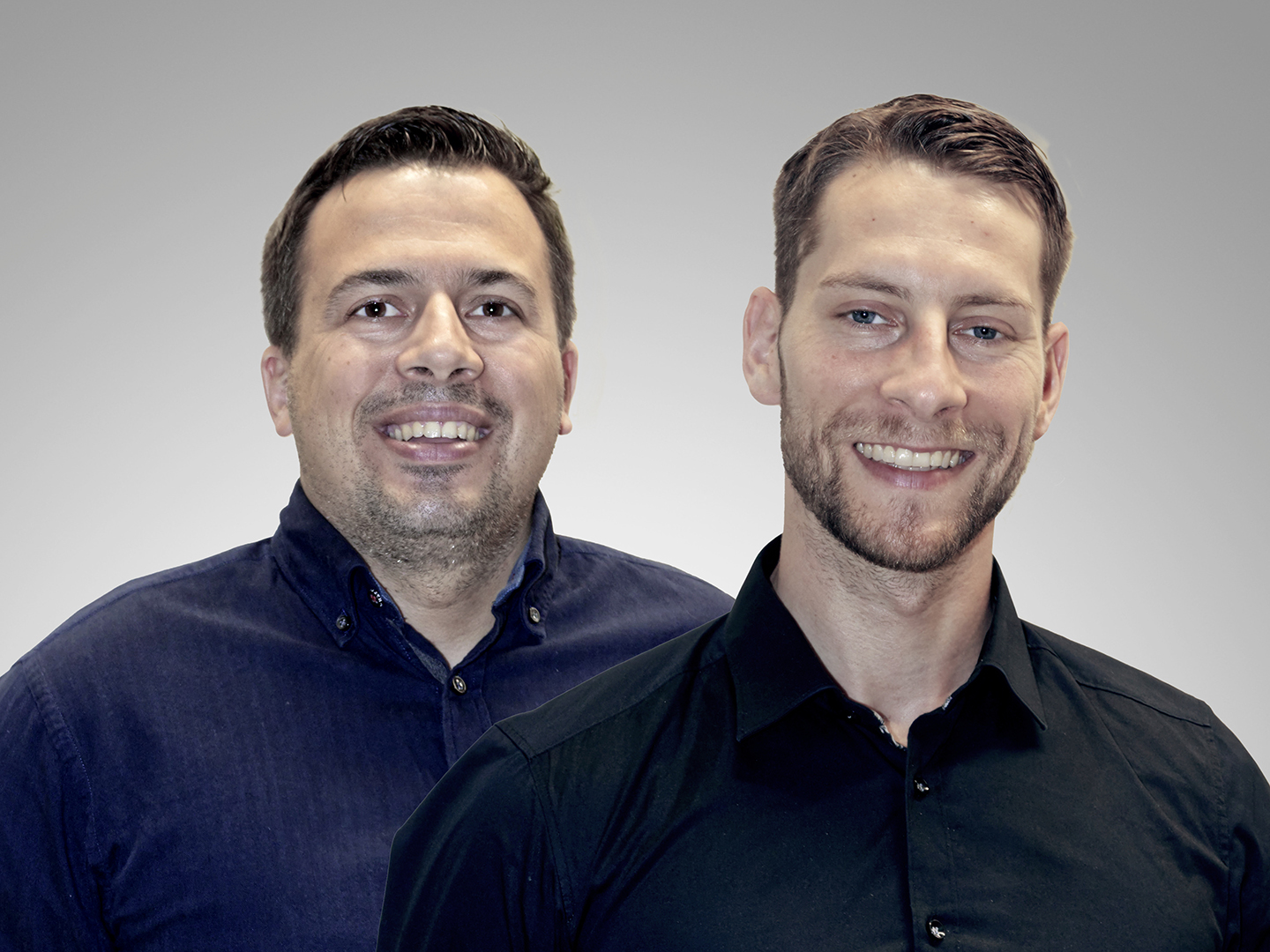
As scientists at MPI-CEC, you work in fundamental research and are involved in the research project in the context of analytics. What has been achieved so far in this area within Carbon2Chem®?
Oliver Hegen: Analytics is an essential part of the work at the Max Planck Institute for Chemical Energy Conversion (MPI-CEC) in Carbon2Chem®, because in order to convert CO2 into a valuable substance as effectively as possible, we first of all need to know what exactly is in the industrial gases. For this we employ established methods such as high-sensitivity gas chromatography (GC) as well as experimental methods like proton transfer mass spectrometry (PTR-MS). We use both techniques in our mobile analysis laboratory, the HügaProp container, and in laboratory 5 in the Carbon2Chem® technical center. While the HügaProp container specializes in analyzing the raw gases, lab 5 is designed for the qualitative and quantitative detection of all main, secondary and trace components in the purified gases. In addition to measuring the real gases, we can also simulate the exact composition of industrial gases at the gas generator in Oberhausen. In the process, we look at how individual compounds influence the reactor or the catalyst installed in it.
Julian Schittkowski: At MPI-CEC, not only do we focus on analytics, we are also involved in fundamental research into how we can reuse CO2 meaningfully. In the newly built Carbon2Chem® lab at the Fraunhofer UMSICHT Oberhausen site, we were able to gain some insights into how the catalyst behaves during the methanol synthesis. Different issues are being investigated at different plants and specially developed measuring concepts have been established for this. At the same time, we see our role in Carbon2Chem® not just in fundamental research or gas analysis, but also as a service provider to all project partners in the characterization of liquids and solids by using our capabilities to support other lighthouse projects as best we can.
What have been the highlights?
Oliver Hegen: Definitely the commissioning of lab 5 in the Carbon2Chem® technical center and the first results that emerged from the measurements. It is always impressive to see what a team of specialists can achieve. The results from the purified gases that we produce in lab 5 are essential to the entire project. They provide us with feedback on how the gas purification works and information about any unusual reactions in the course of the methanol synthesis in the test plants of our project partners.
Julian Schittkowski: The most important milestone for me in the project was the construction of the Carbon2Chem® lab in Oberhausen which provided the infrastructure to successfully commission catalyst test benches from MPI-CEC and Fraunhofer UMSICHT. When investigating the poisoning effects of trace components on the catalyst, we obtained particularly interesting results, which we could then publish.
What were the biggest challenges?
Oliver Hegen: Moving the HügaProp container from the Thyssenkrupp steel mill site to the Carbon2Chem® site in Duisburg. In phase 1 of the project, we investigated the raw gases directly at the steel mill. When the technical center was commissioned it was also logical to move the mobile analysis container. Even though it was only a few kilometers as the crow flies from the former location at the steel mill to the technical center, getting the container to its final site was quite stressful and required a great deal of organizational effort.
Julian Schittkowski: One huge challenge when testing in newly constructed or relocated plants is always the ability to compare. To obtain reproducible results from measurements, sometimes across different test plants, it is necessary to carry out a detailed examination and optimization of each plant right at the start. Despite various hurdles, we were able to overcome this challenge together so that we can now compare all the plants, even though they are designed differently and test different things.
What are the next steps?
Oliver Hegen: We are currently establishing a measurement methodology to enable gas sampling locally at various sites at the Carbon2Chem® technical center. To do this, we are combining state-of-the-art technology with our expertise in industrial gases that we have acquired over the years in this field. Furthermore, we are expanding our research in liquid analytics, especially on methanol, to provide our project partners with further insights. In this way, we can improve methanol synthesis and make even better use of CO2 in the future. Last but not least, we have committed ourselves to automating purified gas analysis in lab 5 as much as possible, so that we can detect fluctuations in gas quality early on and pass them on the project partners.
Julian Schittkowski: Where is the best place to start? Our main goal is to gather a complete picture of the basic process of methanol synthesis from industrial gases. The individual aspects all play a role here, such as the poisoning we observe with individual trace components, catalyst activation, basic reaction parameters such as temperature, pressure and gas composition, and utilizing unconverted reactants. The knowledge gained also needs to be transferred from the laboratory scale to larger plants or pilot plants.