Stahl-Innovationspreis 2018
Micro Steam Turbine Receives Award
On June 13, 2018, Fraunhofer UMSICHT and TURBONIK GmbH were named as joint recipients of the Stahl-Innovationspreis (Steel Innovation Prize) in Berlin. Their project “Highly efficient and oil-free stainless-steel micro steam turbines for independent power generation” took first place in the “Products” category, out of a total of 561 submissions.
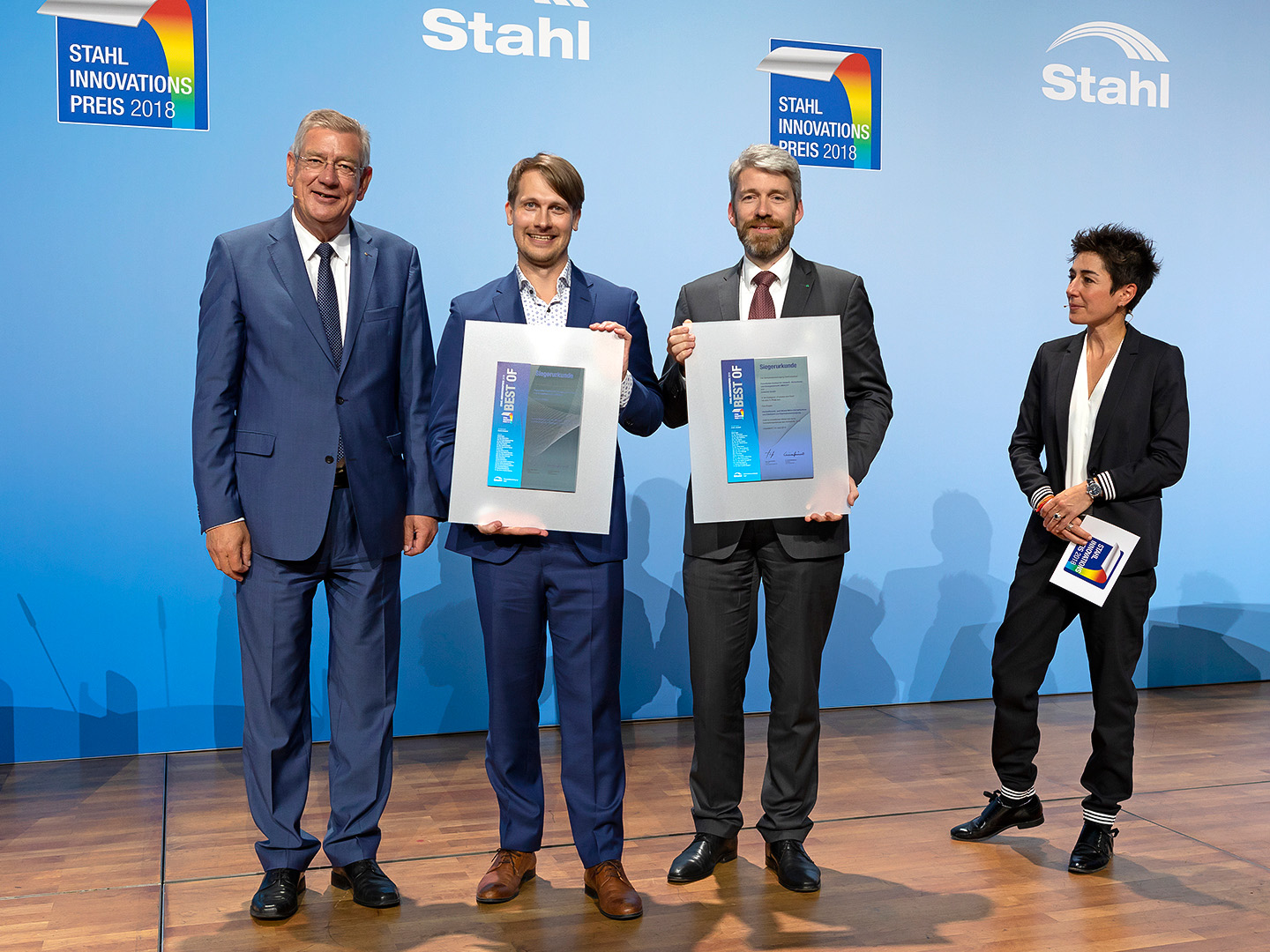
For the eleventh time, the steel industry in Germany recognized outstanding innovations in the area of steel. Three prizes were awarded in each of the four categories: “Steel in Construction,” “Steel Products,” “Steel Design,” and “Steel in Research and Development.” With a total of 561 projects submitted, the competition for this year’s innovation prize included researchers, tradespeople, engineers, designers and architects from all over Germany. Fraunhofer UMSICHT and TURBONIK GmbH, a spin-off of the research institute founded in 2017, impressed the judges with their development of an innovative micro steam turbine, taking first place in their category of “Steel Products.”
Optimizing the use of steam energy
High energy consumption represents a large cost factor for the industry. The micro steam turbine uses process steam, which generates resource-conserving and cost-effective electricity – even with small steam volumes. The new turbine technology is up to 40 percent more efficient than conventional steam turbines in the same output range (up to 300 kWel). This is due to eliminating the gear unit, which in turn allows for very high speeds. In addition, it eliminates high-maintenance, ecologically unfriendly oil lubrication. Even in single-shift operation, the turbine’s low maintenance costs and high efficiency can often cut electricity costs in half. Since the turbine technology is easily integrated into existing plants and systems, it can be used anywhere that boilers have been installed for steam production. For operations that use steam, such as in the pharmaceutical, food and textile industry, integrating micro steam turbines makes it possible to significantly reduce energy costs even for small plants.
Turbine technology implemented in a pilot project
TURBONIK GmbH was founded in 2017 as a spinoff by Fraunhofer UMSICHT employees. The groundwork for the turbine technology was laid and developed in a project by the Oberhausen-based research institute. The first micro steam turbine is being used as part of a pilot project for Energieversorgung Oberhausen AG (evo), where it is used for district heat venting and replaces a pressure reduction valve in the steam system. The turbine is driven by steam, which regulates steam pressure while also generating electricity. The turbine produces 300,000 kWh of electricity per year, which corresponds to the annual consumption of about 60 to 75 four-person households. Energy costs are significantly reduced by this resource-conserving electricity generation, which saves about 90 tons of carbon dioxide a year.
Last modified: