High pressure technology
With new processes for bacteria-free materials and germ-free food
Bacteria like to romp around on plastic components such as light switches, in water pipes or even on medical equipment. This is remedied by germicidal materials such as copper, which is worked into the plastics, or special antibacterial coatings. Fraunhofer UMSICHT has developed new ways to reduce the growth of bacteria on surfaces: This is done either by impregnating antimicrobial agents into layers of polymers near the surface or by preventing the formation of a biofilm by preventing communication between the bacteria. The processes are continuously being developed and tested in application - for the consumer sector, medical technology, technical applications and the food industry.
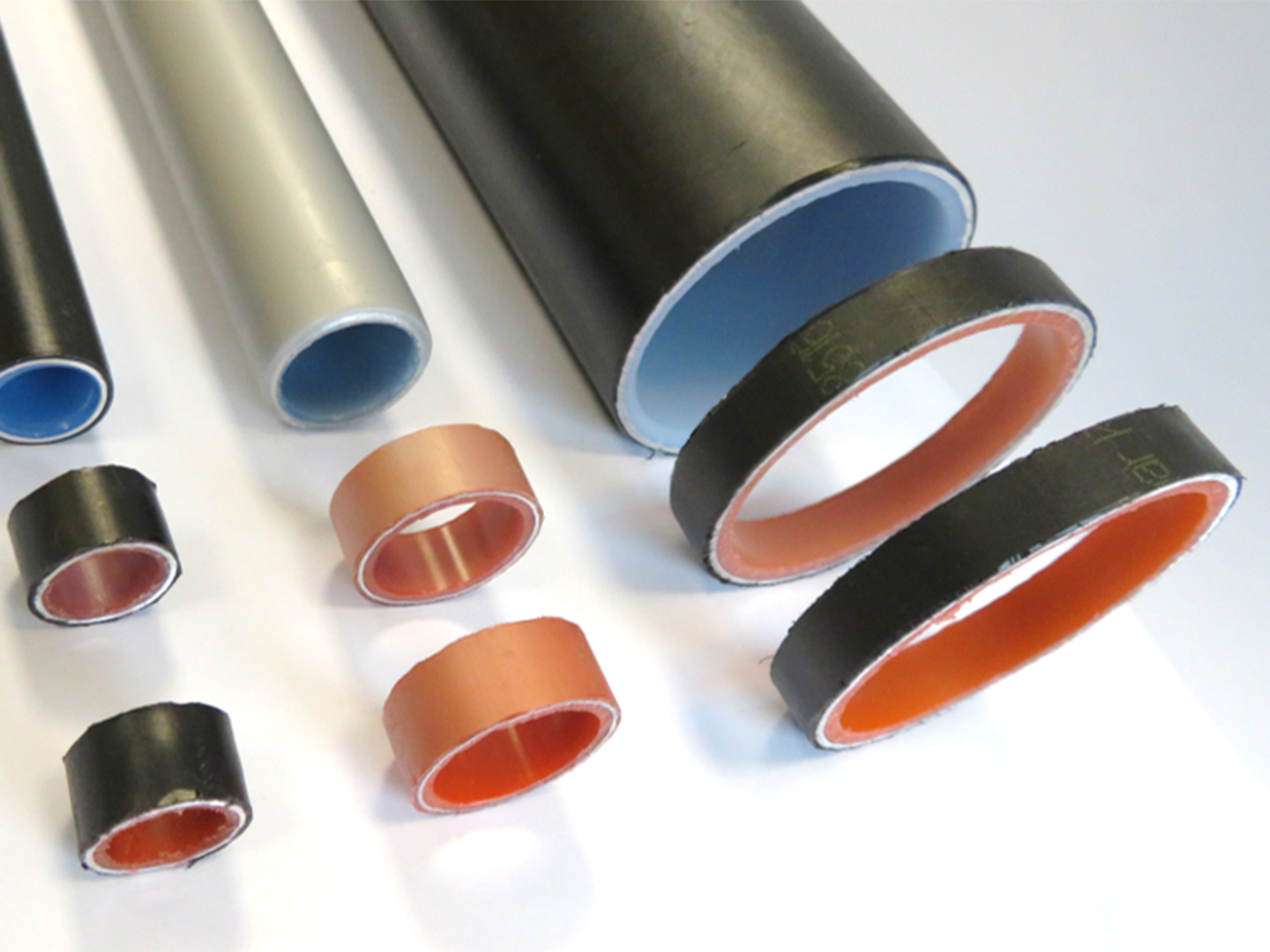
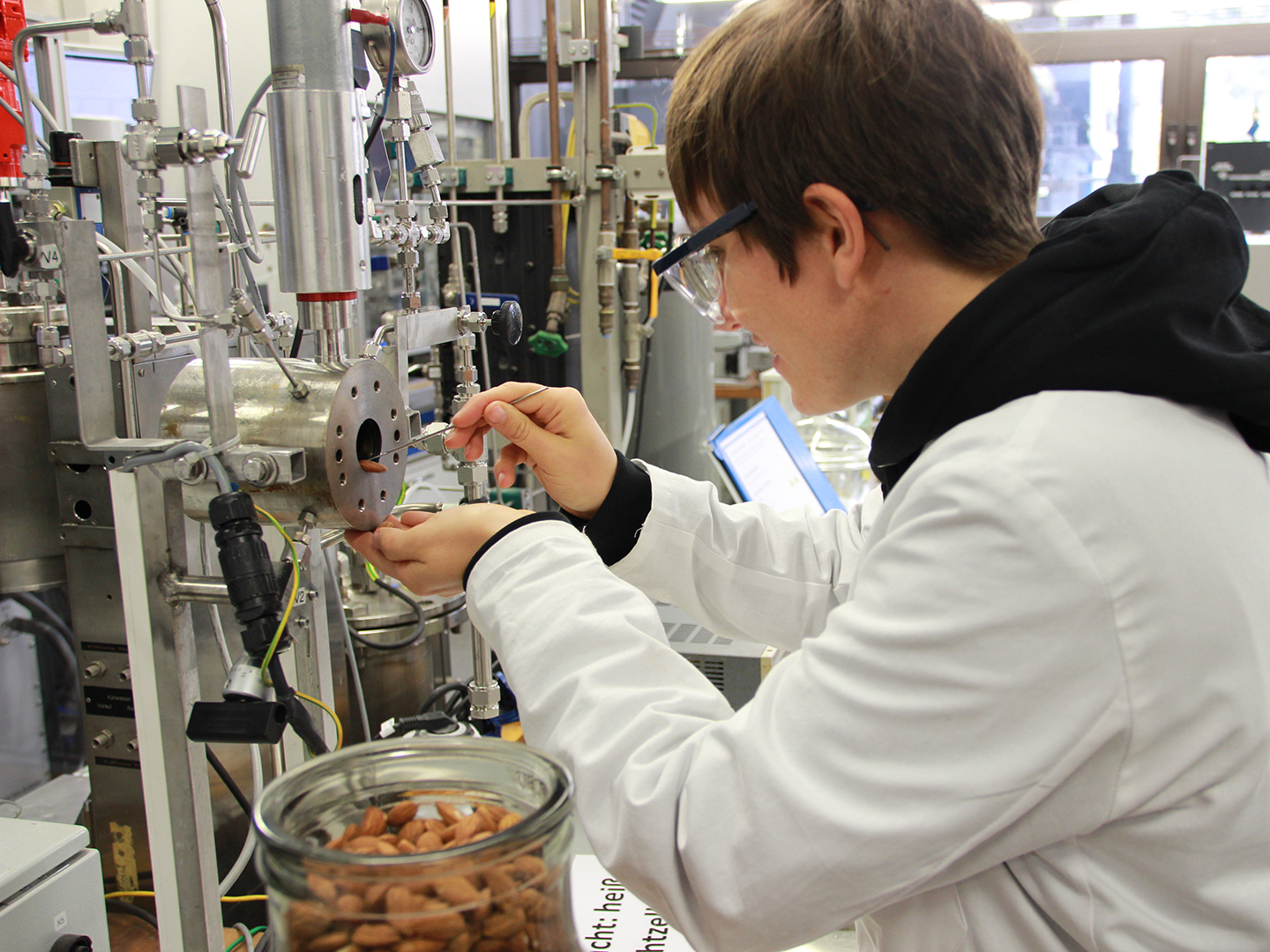
Fraunhofer UMSICHT has been researching the antibacterial impregnation of materials, especially plastics, for ten years. Through cooperation with industry, a broad know-how has been developed, which the researchers are now testing in new application areas and come up with promising solutions. One of the aims is to develop environmentally-friendly alternatives to antibacterial but toxic agents or to very cost-intensive materials such as copper. The advantage of the impregnation process is that only minimal amounts of the antimicrobial agent have to be added and that it is also possible to retrofit the finished component. Another process addresses surfaces on which biofilms can form; these include medical equipment or water pipes. Here the communication between the bacteria can be specifically disturbed, which effectively prevents the formation of biofilms.
Impregnating plastics using high pressure technology
In principle, there are two ways of providing plastics with special functions: Either the desired additives are introduced into the product by compounding, or the active ingredients are applied to the product by means of subsequent surface coating. The subsequent coating makes it possible, for example, for an antibacterial effect to develop exactly where it is supposed to work: on the surface. To this end, Fraunhofer UMSICHT has developed a process that impregnates polymer surfaces with the aid of supercritical carbon dioxide. Supercritical carbon dioxide is ideal for impregnation because it can penetrate a surface as easily as gas and at the same time has the density of a liquid. In addition, carbon dioxide is neither flammable nor toxic, is readily available and inexpensive.
Bacteria removed within one hour
For consumer applications such as light switches, nano- and micro-scale silver particles are introduced during impregnation with supercritical carbon dioxide. This stops bacteria from multiplying. The supercritical carbon dioxide opens up the polymer structure and enables mass transport to the surface. “Tests showed that after just one hour all bacteria were removed from the surface of a previously microbacterially contaminated light switch,“ explains Nils Mölders, Head of the Material Systems and High Pressure Technology Department at Fraunhofer UMSICHT. So-called leaching tests were just as positive, since the silver particles do not wash out according to common standards (DIN-EN 71-3).1
Interrupting communication between bacteria
For sensitive areas of application such as medical technology or drinking water installations, the Fraunhofer researchers rely on “quorum quenching natural substances“ to avoid nanoparticles and silver salts. The aim is not to kill bacteria that have already formed, but to prevent communication between the bacteria in advance so that no bacterial biofilm is formed in the first place. “We use various natural substances that have the property of occupying the receptors of the bacteria and thus preventing communication and thus their harmful effect,“ explains Karen Fuchs from Fraunhofer UMSICHT. The substances are environmentally friendly and not dangerous for humans or animals. They are therefore also suitable for shipbuilding, where biocidal antifouling paints are currently still in use. The natural substances are microencapsulated for immobilization or introduced into the desired material surfaces by means of high-pressure impregnation, for example in paint formulations or drinking water pipes. Initial successful tests have been carried out on a laboratory scale at Fraunhofer UMSICHT, and field trials for boat paints are in preparation. The identification and validation of the quorum quenching active substances is carried out in cooperation with the Goethe University Frankfurt, the Gutenberg University Mainz and the industrial partners Brill & Partner and KEBOS.
Against pathogenic germs on food
Some foods are susceptible to germs, which means that harmful micro-organisms such as salmonella can settle on them during processing. In recent years, especially foods with low water activity have been increasingly affected by recalls due to contamination. These foods include almonds, peanuts, nut patties, dried fruits and vegetables, dried meat, dairy products (e. g. milk powder) as well as dried teas, herbs and spices. For the food industry, this global development results in an urgent need for decontamination technologies that can be used internationally and guarantee high food quality in addition to food safety. Together with partners from the University of Alberta (Canada), Fraunhofer UMSICHT is developing a process to kill pathogenic microorganisms on food by using compressed carbon dioxide.
Antimicrobial agents from nature
The researchers have already succeeded in decontaminating almonds on a laboratory scale using antimicrobial oils and supercritical carbon dioxide. At the same time, the impregnation makes the almonds resistant to germs and their quality is not impaired. “The oils used are exclusively vegetable extracts and CO2 extracted, so that during the impregnation process, the oil dissolves back into the compressed CO2 and penetrates into the surface to be impregnated and achieves its effect,“ explains Karen Fuchs. The use of CO2 has the further advantage that it can be separated from the almonds without leaving any residue and recycled after the process. The next goal is to transfer the process to other foodstuffs.
Fraunhofer UMSICHT is looking for cooperation partners to further develop the processes and to test new fields of application. Are you interested? Then please contact us!
1 Mölders, Nils; Renner, Manfred; Errenst, Cornelia; Weidner, Eckhard (2018); Incorporation of antibacterial active additives inside polycarbonate surfaces by using compressed carbon dioxide as transport aid; in: The Journal of Supercritical Fluids; Volume 132, February 2018, Pages 83-90
More Information
Competencies of the Fraunhofer UMSICHT
Last modified: