Carbon2Chem®
Die Stahlproduktion klimafreundlich gestalten
Die Stahlproduktion klimafreundlich gestalten – mit dieser Zielsetzung ist Carbon2Chem® im März 2016 gestartet. Die erste Phase des vom Bundesministerium für Bildung und Forschung (BMBF) geförderten Verbundprojektes wurde im Mai 2020 abgeschlossen. In diesen vier Jahren sind Verfahrenskonzepte entstanden, mit deren Hilfe die CO2-haltigen Abgase von Deutschlands größtem Stahlwerk aufgefangen, gereinigt und mittels »grünem« Wasserstoff in Grundstoffe für Chemikalien, Kraftstoffe oder Dünger umgewandelt werden können. In der zweiten Projektphase werden diese Konzepte für die großtechnische Umsetzung validiert.
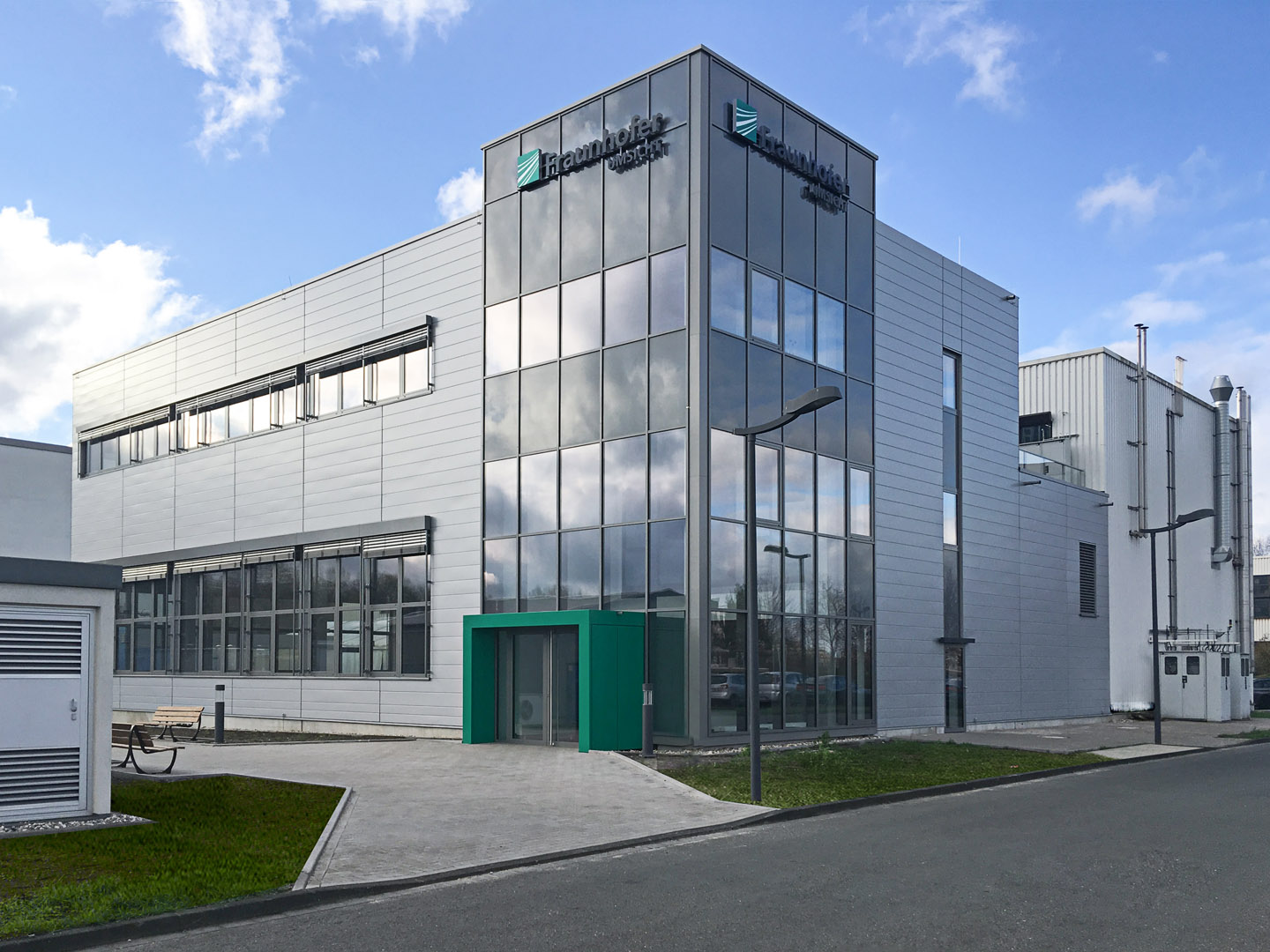
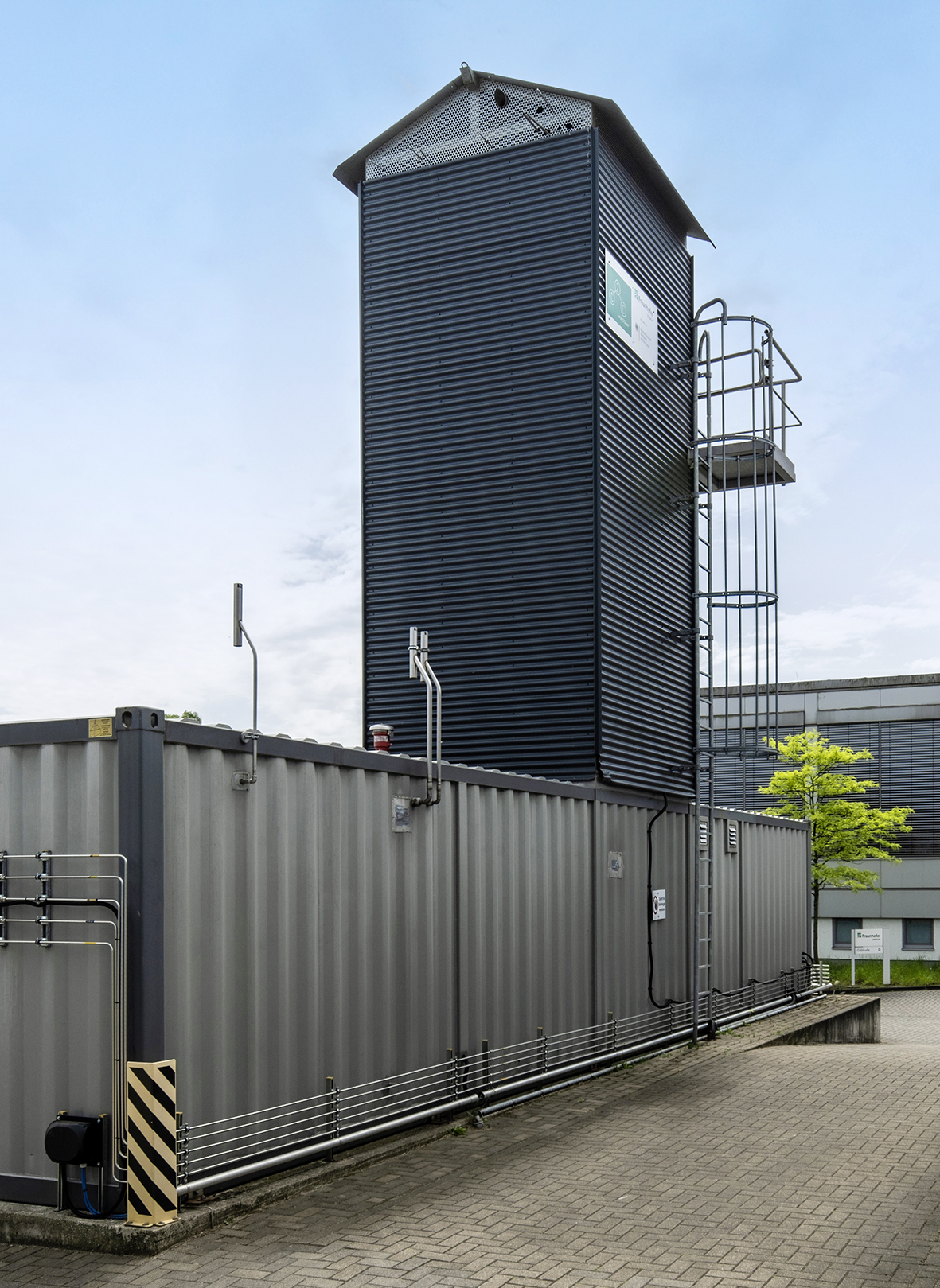
»Das Konsortium aus Grundlagenforschung, anwendungsorientierter Forschung und Entwicklung sowie Industrie, das hinter Carbon2Chem® steht, hat sich bewährt«, lautet die Zwischenbilanz von Geschäftsstellenleiter Dr.-Ing. Torsten Müller. »Die Partner arbeiten engagiert und zielorientiert zusammen. Gemeinsam haben sie erreicht, dass das Projekt ein Aushängeschild der nationalen Energieforschung ist.« Insgesamt sind knapp 20 Unternehmen und Forschungseinrichtungen involviert. Ihre Koordination liegt bei dem Max-Planck-Institut für Chemische Energiekonversion, dem Fraunhofer-Institut für Umwelt-, Sicherheits- und Energietechnik UMSICHT und thyssenkrupp Carbon2Chem GmbH.
Carbon2Chem®-Infrastruktur: Orte gemeinsamer Forschung und Entwicklung
Forschung und Entwicklung finden u. a. im gemeinsamen Technikum am thyssenkrupp-Standort in Duisburg statt. 2018 eröffnet, bietet es durch die Nähe zum Stahlwerk direkten Zugang zu realen Hüttengasen und die Möglichkeit, Versuche unter Industriebedingungen durchzuführen. Zudem betreiben das Max-Planck-Institut für Chemische Energiekonversion und Fraunhofer UMSICHT das Anfang 2019 eingeweihte Projektlabor in Oberhausen. Hier wird gemeinsam an Verfahren zur Gasreinigung sowie zur Produktion von Methanol und höheren Alkoholen geforscht.
Ein weiterer Baustein der Carbon2Chem®-Infrastruktur ist ebenfalls 2019 in Betrieb gegangen: In der Methanol-Pilotanlage in Oberhausen laufen Versuche, um die Produktion von Methanol aus Hüttengas verfahrenstechnisch simulieren zu können. Die Anlage zieht in der zweiten Projektphase ans Technikum in Duisburg und wird dort bis zu 75 Liter Rohmethanol am Tag aus den Hüttengasen produzieren.
Forschungsergebnisse: Von der Wasserelektrolyse über die Gasreinigung bis zur Synthese
An diesen Orten sind in der ersten Förderphase wichtige Detailergebnisse erzielt worden. Es konnte u. a. gezeigt werden, dass der aus Stahlwerksabgasen gewonnene Wasserstoff gereinigt direkt für chemisch-katalytische Prozesse eingesetzt werden kann. Eine weitere Erkenntnis: Die alkalische Elektrolyse lässt sich auch dynamisch betreiben – und zwar ohne Alterungseffekte oder Effizienzverluste. Dynamischer Betrieb heißt in diesem Zusammenhang, dass die Anlage entsprechend dem Angebot an erneuerbarem Strom geregelt wird.
Im Bereich der Gasreinigung konnten neue Strategien entwickelt und optimiert werden. Eine entsprechende Anlage wurde gebaut und erfolgreich betrieben. Sie setzt auf Druckwechseladsorption, Gaswäsche und Verdichtung. Darüber hinaus liegen Experimentalergebnisse zur thermokatalytischen und plasmakatalytischen Sauerstoffentfernung (DeOxo-Verfahren) vor.
Ende 2018 ist es im Technikum erstmals gelungen, Methanol und Ammoniak im Labormaßstab aus realem Hüttengas zu erzeugen. In der zweiten Projektphase geht es darum, zu zeigen, dass diese Verfahren auch im Großen stabil funktionieren, und die Basis für einen emissionsarmen Betrieb des Stahlwerks in Duisburg zu legen. Dafür stellt das BMBF bis 2024 weitere 75 Millionen Euro zur Verfügung.
Letzte Änderung: